HPMC in drymix mortar
Hydroxypropyl Methylcellulose (HPMC) in Drymix Mortar: Properties, Applications, and Benefits
Introduction HPMC in drymix mortar:
Drymix mortar, also known as dry mortar or dry-mix mortar, is a blend of various ingredients used in construction to create a ready-to-use mixture for various applications. It typically consists of a combination of cement, sand, and additives. One of the essential additives used in drymix mortar formulations is Hydroxypropyl Methylcellulose (HPMC). In this comprehensive article, we will explore the properties, applications, and benefits of HPMC in drymix mortar.
Section 1: Introduction to HPMC
1.1 What is HPMC?
HPMC, short for Hydroxypropyl Methylcellulose, is a synthetic polymer derived from cellulose. It is a versatile and multifunctional compound widely used in various industries, including the construction sector. HPMC is water-soluble and can be easily dispersed in cold water to form a viscous, gel-like solution.
1.2 Properties of HPMC
HPMC offers a range of unique properties that make it highly suitable for use in drymix mortar:
1.2.1 Water Retention: HPMC has excellent water retention properties, allowing it to retain water within the mortar mixture, even in dry and arid conditions. This property contributes to improved workability and hydration of the mortar.
1.2.2 Thickening: HPMC acts as a thickening agent, enhancing the viscosity of the mortar mixture. This increased viscosity helps in reducing the risk of segregation and improving the consistency of the mix.
1.2.3 Binding: HPMC improves the binding and adhesion properties of drymix mortar. It forms a film on the surface of the mortar particles, which enhances the bond strength and durability of the mortar.
1.2.4 Rheological Control: HPMC offers rheological control, allowing the adjustment of the mortar’s flow and setting time. This enables the mortar to meet specific application requirements.
1.2.5 Retardation: HPMC can act as a retarding agent, slowing down the setting time of the mortar. This property is particularly useful in hot weather conditions or when extended working time is needed.
1.2.6 Improved Open Time: The addition of HPMC in drymix mortar extends the open time, making it easier for workers to apply the mortar without concerns about it drying too quickly.
1.2.7 Crack Resistance: HPMC enhances the mortar’s resistance to cracking, which is crucial for the long-term structural integrity of the construction.
1.3 Production of HPMC
HPMC is manufactured through a series of chemical processes involving cellulose extraction from wood or cotton. The extracted cellulose is then chemically modified by introducing hydroxypropyl and methyl groups. The degree of substitution (DS) of these groups can vary, resulting in different grades of HPMC with specific properties.
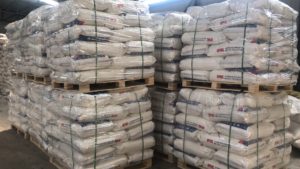
Section 2: Applications of HPMC in Drymix Mortar
2.1 HPMC in Tile Adhesives
HPMC is commonly used in tile adhesives to improve their workability and bond strength. In tile adhesive formulations, HPMC acts as a water retention agent, allowing the adhesive to maintain moisture for a more extended period, ensuring strong adhesion to the substrate. It also provides the necessary consistency for easy application and reduces the risk of tile slippage or sagging during installation.
2.2 HPMC in Plaster and Stucco
In plaster and stucco applications, HPMC serves as a key additive to enhance workability and adhesion. It helps in reducing cracking and improving the consistency of the plaster or stucco mixture. Additionally, HPMC aids in achieving a smooth finish and provides rheological control, making it easier for workers to apply and shape the material on walls and ceilings.
2.3 HPMC in Masonry Mortar
Masonry mortar formulations often benefit from the addition of HPMC. It improves the cohesion of the mortar, allowing it to bond well with bricks or blocks. HPMC’s water retention properties help prevent premature drying of the mortar, ensuring a strong bond and preventing cracks in the masonry work. The extended open time provided by HPMC allows masons to work efficiently without rushing to complete the task.
2.4 HPMC in Self-Leveling Compounds
Self-leveling compounds are used to create flat and smooth surfaces for flooring installations. HPMC is employed in these compounds to control their flow and self-leveling properties. It ensures that the mixture spreads evenly, providing a uniform and level surface. HPMC’s water retention properties are essential in preventing the compound from drying out too quickly, which can result in uneven surfaces.
2.5 HPMC in EIFS (Exterior Insulation and Finish Systems)
Exterior Insulation and Finish Systems (EIFS) are used for exterior wall insulation and finishing. HPMC is used in EIFS formulations to provide adhesion, water resistance, and workability. It helps the system adhere to the building’s exterior, enhancing its durability and appearance. Additionally, HPMC contributes to the system’s flexibility, allowing it to withstand environmental stresses and temperature variations.
2.6 HPMC in Grouts
Grouts are used to fill gaps and voids in various construction applications, such as tile grouting, concrete repair, and masonry repair. HPMC plays a vital role in grout formulations by improving their flow properties, adhesion, and water retention. This ensures that the grout remains intact and securely bonds with the surrounding surfaces, preventing leaks and enhancing structural integrity.
Section 3: Benefits of Using HPMC in Drymix Mortar
3.1 Improved Workability
One of the primary benefits of incorporating HPMC in drymix mortar is its ability to enhance workability. HPMC acts as a thickening agent, reducing the risk of segregation and providing a smooth and consistent mixture. This makes it easier for construction workers to apply and shape the mortar as needed, resulting in a more efficient and aesthetically pleasing end product.
3.2 Water Retention
HPMC’s exceptional water retention properties are advantageous in drymix mortar. It prevents the rapid evaporation of water, ensuring that the mortar remains adequately hydrated during the curing process. This leads to better adhesion, reduced cracking, and overall improved performance of the mortar, even in hot and dry conditions.
3.3 Enhanced Adhesion
HPMC forms a film on the surface of mortar particles, which enhances the adhesion properties of the drymix mortar. This is particularly valuable in applications like tile adhesives and masonry mortar, where a strong bond with the substrate is essential for the long-term integrity of the construction.
3.4 Reduced Cracking
Cracking in mortar can be a significant concern, as it compromises the structural integrity of the construction. HPMC helps mitigate this issue by improving the mortar’s resistance to cracking. This is especially important in applications where the mortar may be subjected to various stresses, such as exterior insulation and finish systems or self-leveling compounds.
3.5 Extended Open Time
The addition of HPMC in drymix mortar formulations extends the open time, allowing construction workers more time to apply and adjust the mortar without the fear of it drying too quickly. This is particularly valuable in applications where precision and meticulous workmanship are required.
3.6 Improved Durability
HPMC contributes to the overall durability of the construction. Its ability to control the mortar’s rheology, provide water retention, and enhance adhesion results in a more robust and long-lasting structure. This durability is especially important in projects where longevity and resistance to environmental factors are key considerations.
Section 4: Formulation Considerations
4.1 Dosage
The dosage of HPMC in drymix mortar formulations is a critical factor. The optimal dosage may vary depending on the specific application and the desired properties. Typically, HPMC is added in the range of 0.1% to 0.5% of the dry mortar weight, but this can be adjusted as needed to achieve the desired results.
4.2 Compatibility with Other Additives
In many cases, drymix mortar formulations include a combination of additives to achieve the desired performance characteristics. It’s essential to ensure that HPMC is compatible with other additives used in the mixture. Compatibility testing should be conducted to avoid any adverse interactions that could compromise the mortar’s performance.
4.3 Particle Size and Quality
The particle size and quality of HPMC can impact its performance in drymix mortar. Fine and uniform particle sizes are typically preferred, as they disperse more evenly in the mixture. Additionally, the quality of HPMC, including its degree of substitution (DS), can influence its properties and effectiveness in the mortar.
4.4 Mixing Procedure
The proper mixing of HPMC in drymix mortar is essential for achieving consistent and desirable results. HPMC should be added gradually to the dry mix while mixing, and it should be dispersed thoroughly to ensure even distribution within the mortar. The mixing procedure may vary depending on the specific application and equipment used.
Section 5: Environmental Considerations
5.1 Sustainability
Sustainability is a crucial consideration in modern construction practices. HPMC, being derived from cellulose, is generally considered an environmentally friendly additive. Additionally, its use in drymix mortar can lead to more efficient construction practices, reducing waste and improving the durability of structures, which, in turn, contributes to sustainability.
5.2 Reduced Water Usage
The water retention properties of HPMC in drymix mortar lead to reduced water usage during construction. This is beneficial for conserving water resources and aligns with sustainable building practices.
5.3 Energy Efficiency
The improved workability and extended open time provided by HPMC can result in energy savings on construction sites. When workers have more time to complete tasks, it can reduce the need for overtime work and the associated energy consumption.
Section 6: Challenges and Considerations
6.1 Quality Control
Maintaining consistent quality in drymix mortar formulations containing HPMC is essential. Variations in HPMC quality, dosage, or mixing procedures can lead to inconsistent performance. Quality control measures should be implemented to ensure that the mortar meets the desired specifications.
6.2 Compatibility Issues
Compatibility issues can arise when HPMC interacts with other additives or ingredients in the mortar mixture. It is crucial to conduct compatibility tests and work closely with suppliers to ensure that the combination of additives used in the formulation does not lead to adverse effects.
6.3 Application Techniques
The application of drymix mortar with HPMC may require specific techniques and tools to achieve the best results. Workers should be trained in the proper application methods to ensure that the mortar is used effectively.
6.4 Cost Considerations
The cost of HPMC can vary depending on factors such as grade, quality, and supplier. It’s important to consider the cost of HPMC in relation to the overall cost of the construction project and the benefits it provides in terms of improved performance and durability.
Section 7: Future Trends and Developments
7.1 Sustainable Additives
The construction industry is increasingly focusing on sustainability and environmentally friendly practices. Future developments in the use of HPMC may involve more sustainable sourcing and manufacturing processes, further aligning with green building principles.
7.2 Advanced Blends
Researchers and manufacturers are likely to explore advanced blends of HPMC with other additives to create tailored solutions for specific construction applications. These blends may offer enhanced performance characteristics and improved compatibility.
7.3 Digital Integration
The construction industry is becoming more digitized, and the use of digital tools and technologies in mortar application is expected to increase. HPMC may play a role in digitally integrated construction practices, ensuring that mortar mixtures are precisely controlled and optimized.
7.4 Recycling and Reuse
As sustainability becomes a more significant concern, the recycling and reuse of construction materials may become more prevalent. HPMC can play a role in creating mortar mixtures that are easier to disassemble and reuse, reducing waste and conserving resources.
Section 8: Conclusion
In conclusion, Hydroxypropyl Methylcellulose (HPMC) is a versatile and essential additive in drymix mortar used in various construction applications. Its properties, including water retention, thickening, binding, rheological control, and retardation, make it a valuable component in improving workability, adhesion, and durability of mortar mixtures. The benefits of using HPMC in drymix mortar include improved workability, water retention, adhesion, reduced cracking, extended open time, and enhanced durability.
Proper dosage, compatibility testing, and quality control are critical considerations when using HPMC in mortar formulations. As the construction industry evolves to focus on sustainability and advanced building practices, HPMC is expected to play a significant role in shaping the future of drymix mortar applications.
As the demand for high-performance and environmentally friendly construction materials continues to grow, HPMC will likely remain a key component in enhancing the quality and sustainability of construction projects. Its versatility and adaptability to various applications make it a valuable tool for architects, engineers, and construction professionals seeking to create durable and reliable structures.
In summary, Hydroxypropyl Methylcellulose (HPMC) in drymix mortar is a fundamental ingredient that contributes to the quality, workability, and sustainability of modern construction practices. Its use enhances the performance of mortar mixtures and aligns with the evolving demands of the construction industry, making it a crucial component in the development of durable and sustainable structures.