What effect does hydroxypropyl methylcellulose have on cement mortar?
Hydroxypropylmethylcellulose (HPMC) is a cellulose ether derivative commonly used as a thickener and stabilizer in various industries, including the construction industry. When added to cement mortars, HPMC can have a variety of significant effects on its properties and performance.
Overview of Hydroxypropyl Methylcellulose (HPMC)
Hydroxypropyl methylcellulose, often abbreviated as HPMC, is a water-soluble polymer derived from cellulose. It is widely used in the construction industry as an additive to cement-based materials to improve their performance in all aspects. HPMC is well known for its ability to modify the rheological and mechanical properties of cement mortars.
Water retention
One of the key roles of HPMC in cement mortars is its effect on water retention. HPMC is hydrophilic, meaning it has a strong affinity for water. When added to mortar, it forms a thin film around the cement particles, preventing rapid loss of moisture. This enhanced water retention improves workability and prolongs hydration of the cement, thereby helping to improve overall performance.
Processability
Workability is an important property of mortar that affects how easy it is to handle and apply. HPMC acts as a rheology modifier to improve the workability of cement mortar. The interaction of the polymer with water creates a lubrication effect that reduces friction between particles, making the mortar easier to mix, spread and form.
solidification time
The setting time of cement mortar is affected by many factors, and HPMC can retard the setting. The water-retaining properties of HPMC slow down water evaporation and extend the time it takes for cement to hydrate. This can be advantageous in certain construction applications where longer setting times are required.
Strength development
Although HPMC affects setting time, its effect on cement mortar strength development is generally positive. By enhancing water retention and workability, HPMC helps increase cement hydration efficiency, potentially increasing compressive and flexural strength over time.
Improve adhesion
Hydroxypropyl methylcellulose can enhance the adhesion of mortar to various substrates. The film-forming properties of HPMC form a thin layer on the surface, promoting better bonding between the mortar and substrate. This is especially beneficial for applications that require strong adhesion, such as tile installations.
Reduce shrinkage
Shrinkage is a common problem with cement-based materials and can lead to cracks and other durability issues. HPMC reduces shrinkage by maintaining a higher moisture content in the mortar. Improved water retention helps minimize moisture loss during the drying process, reducing the potential for cracks and improving the overall durability of the mortar.
Freeze and thaw resistance
In areas where freeze-thaw cycles are prevalent, the durability of cement mortar may be affected. HPMC improves the freeze-thaw resistance of mortar by improving its workability and reducing water loss during initial curing. This helps prevent damage caused by the expansion of water within the material during freezing.
Tile glue
HPMC is commonly used in tile adhesives to improve the workability, adhesion and durability of mortar. The polymer’s water-retention capabilities are particularly beneficial in tile installation applications where consistent and extended open times are critical.
Rendering and stucco
In plastering and stucco applications, HPMC plays an important role in enhancing the workability and adhesion of the mortar to the substrate. Improved water retention helps achieve a smoother, more even surface, reducing the likelihood of cracking.
Self-leveling underlayment
For self-leveling underlayments, HPMC is used to control the viscosity and flow characteristics of the mortar. The water-retaining properties of the polymer contribute to the material’s self-leveling properties, ensuring a smooth surface.
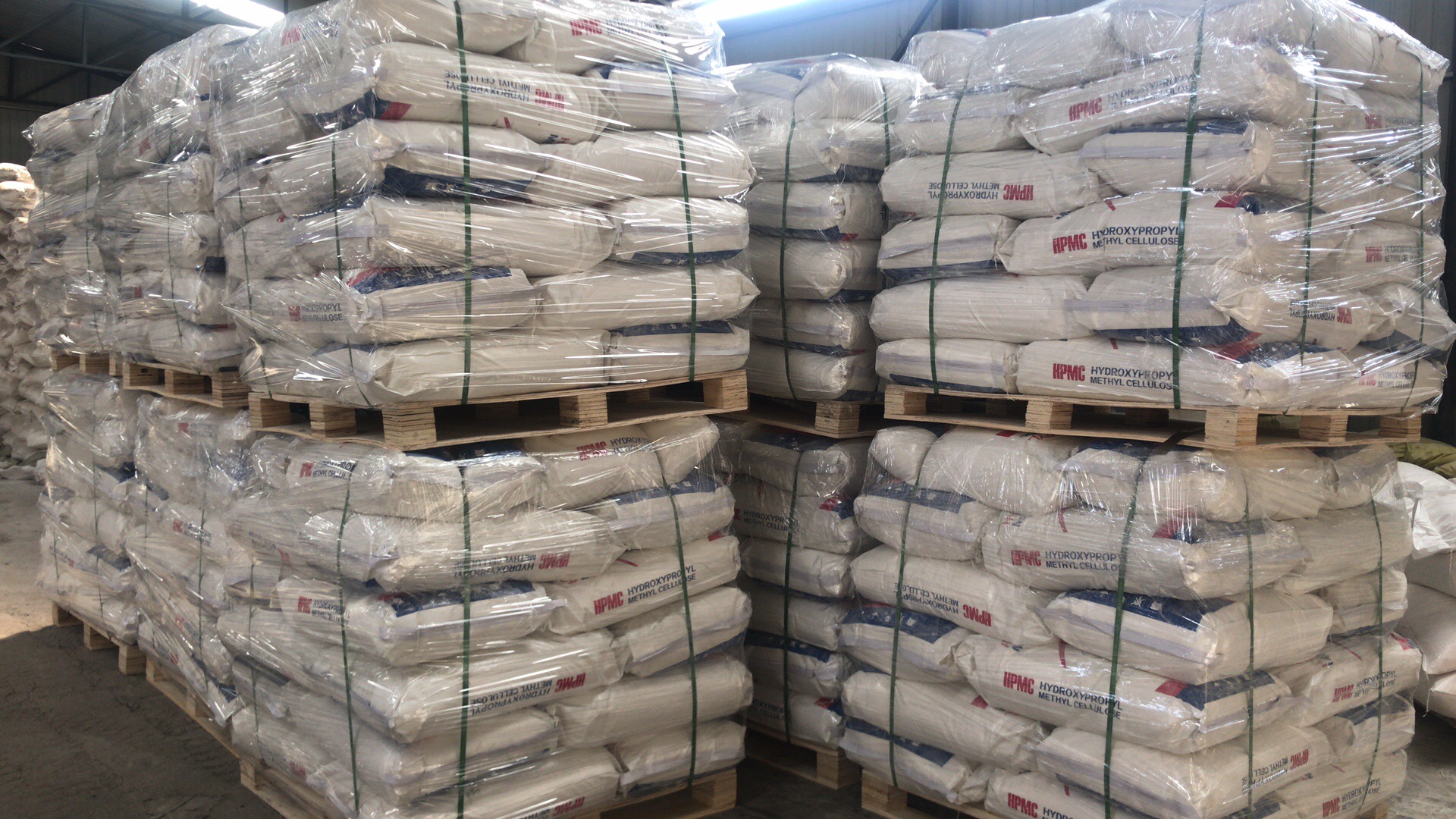
Precautions and Dosage
While HPMC offers a variety of benefits, the correct dosage is critical to achieve the desired results without negatively affecting mortar performance. Excessive use of HPMC can result in long setting times or loss of strength. Manufacturers and contractors must carefully follow recommended dosage guidelines to optimize the benefits of HPMC in cement mortars.
in conclusion
In summary, hydroxypropyl methylcellulose has multifaceted effects on cement mortar, affecting its physical, mechanical and durability properties. From improving workability and water retention to improving adhesion and water resistance, HPMC has good durability and is a valuable additive in the construction industry. As with any construction material, proper understanding of dosage and application techniques is critical to realizing the full potential of HPMC to optimize cement mortar performance.